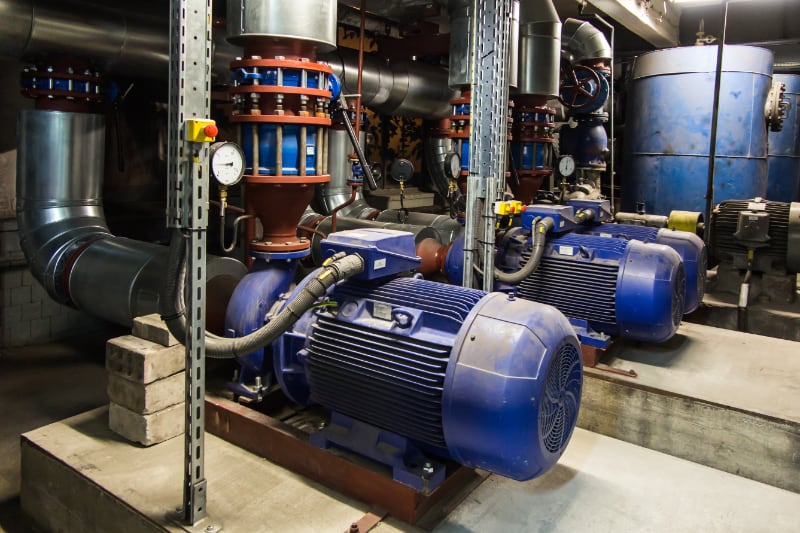
Picked over. Old hat. Dry well. These are all phrases I’ve heard when discussing the possibility of energy savings in electric motor applications within manufacturing facilities. As a manufacturer, what is the best way to understand the current state of optimization of the electric motor loads within a given facility? How can a manufacturing facility optimize their processes (the cake) and realize energy savings by doing so (the icing on the cake)?
Many companies already think critically about energy efficiency, sustainability and power system reliability and resilience. This is important, since statistics from the U.S. Department of Energy indicate a 5-year annual average energy consumption in the U.S. of approximately 3.8T kilowatt-hours, 50% of which (about 2T kWh) was utilized by electric motors. Similar studies show that, in the U.S., industrial manufacturing consumes more than one-third of all electric power produced and that electric motors comprise 55% to 85% of the total electric load within a typical industrial manufacturing facility. Doing some quick math and applying a conservative safety factor (because, as we know, about 44% of all statistics are made up on the spot!), that would mean that on average, electric motors within industrial manufacturing facilities are consuming 700 billion kilowatt-hours of electricity annually.
Now, if just one in every 10 of these electric motors could be optimized to reduce its consumption by 10% (i.e., 10% energy reduction of 10% of the motors operating in the U.S.), the result would be annual energy reduction/savings of 7 billion kilowatt-hours. Not all motors are the same size (power rating) so there are some liberties taken in this estimate.
Finally, at a very attractive rate of $0.07/kWh, and with the above shown reduction of 7B kWh, U.S. manufacturers could save almost $500M collectively in energy costs every year. Where could that money be used and how could freeing up 7B kwh of energy change things? The possibilities are staggering.
In addition, the savings and/or cost avoidance that a manufacturer could realize by optimizing their electric motor control strategy to align with their production goals (aka: process optimization via electric motor control) is even greater. It’s worth noting that there are situations where process optimization may actually result in higher energy costs, but there are financial trade-offs that create compelling reasons to do so, nonetheless. An example of this might be in cooling or freezing a certain food product after production. If the product is not properly cooled or frozen, it may spoil, which would result in poor quality and high scrap rates at a minimum but could result in further issues related to regulatory compliance and hazards to consumers. It may take more energy to further cool the product to avoid these issues, but the trade-off of improved quality and higher production yields is well worth it.
If all of this sounds complicated, don’t worry. FTI is an end-to-end solution provider with a national presence and a diverse range of capabilities that have been developed through years of experience in various manufacturing settings. Our process automation and optimization solutions begin with a holistic assessment of your processes and existing infrastructure. Generally, a measurement of power consumption for common operational conditions is obtained, along with general power quality information to serve as a baseline for outcomes to be measured against. Next, data is correlated to production/operational situations and is coupled with application knowledge from a cross-functional team to determine which applications may provide the most impact in terms of both process improvement and energy savings.
Within FTI, we have a team of more than 2,500 people focused on electrical infrastructure design, industrial controls and automation, specialty systems, renewable energy technologies and power/energy management solutions to work with our customers to drive positive business outcomes.
Picked over. Old hat. Dry well. If you’ve heard these excuses for not looking at process optimization, I encourage you to dig a bit deeper and ask questions about how you can realize energy savings for your organization. Contact us today to let us know how we can help.
If you enjoyed this blog article, please subscribe to stay up to date on the latest industry news from our experts at FTI.