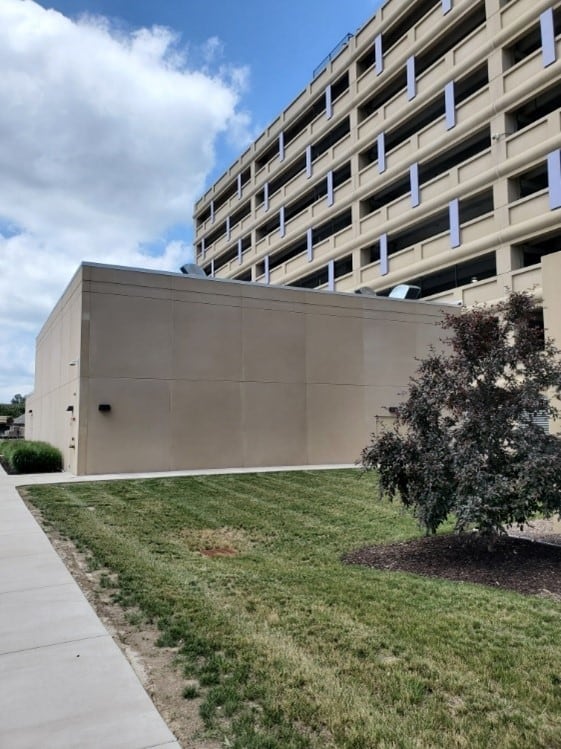
Children’s Wisconsin is a fully integrated health system dedicated to caring for children and teens, and is one of the nation’s top pediatric facilities. Located in Milwaukee, and with roots dating back to 1894, Children’s Wisconsin has continued to grow to serve the children of Milwaukee, the region and the state with a mission of ensuring that the children of Wisconsin will be the healthiest in the nation.
In 2018, Children’s kicked off a multi-year Milwaukee Campus Improvement Project (MCIP) to enhance clinical collaboration and efficiencies, improve the child and family experience and support the use of innovative technologies. As part of this project, FTI was chosen by Children’s and general contractor The Boldt Company to replace four emergency power generation units; two 1.5 meg units in the hospital’s Center Tower and two 1.0 meg units in the East Tower. The current generators were nearing the end of their useful life, so new power generation was needed.
Using our design-assist expertise and extensive knowledge of the Children’s campus based on years of partnerships, FTI examined other options for the hospital’s power needs rather than simply replacing the current generators in the same place. FTI provided the hospital with improved power generation that was relocated to a new, centralized generator plant near the hospital but away from patient care and public areas. Children’s also sought to ensure appropriate power for future campus planning and expansion, which was best enabled in this new location.
An electrical project of this size and with this much at stake cannot be completed without precise and rigorous planning. Led by the superintendent, the project management team created a 30+-page Sequence of Operations (SoO) document which detailed each individual power outage – nearly 60 in all – required to transfer power from the old generators to the new units. Based on the SoO document, user-group meetings were scheduled for every planned outage for all parties involved, including physicians, medical team members and department heads. Initial meetings walked through the proposed shutdowns and reviewed Children’s requirements of what level and duration of outage would be acceptable. Mitigation plans were then built. Second meetings were held for each outage where the schedule and mitigation plans were shared and to confirm approval and sign off by all.
It was crucial that patient care never be compromised due to an outage. FTI’s electrical engineering expertise, healthcare experience and vast knowledge of Children’s facilities enabled us to ensure that each required outage was completed precisely and safely. Throughout the project, unforeseen critical patient needs and weather events took precedence over each outage, with reschedules made and communicated to all.
As the idea for Children’s off-site power generator plant came together, one challenge was how to bring power from the new site to the hospital campus, approximately 1,600 feet, two blocks away. Working at a congested healthcare campus, excavating and installing the entire new duct bank at once was not a feasible option.
Working with the limited project footprint, extensive modeling was used to determine the elevations and required gear connections, analyzing conduit run iterations to determine the best path in the tight space. FTI engineered a route that ran through existing utility lines under a campus road, with individual excavations completed quickly to limit traffic disruption.
With limited on-site space for construction, the project’s duct bank was prefabricated at Excellerate, FTI’s manufacturing division. This decreased on-site labor needs, leading to a safer build in a controlled environment. Once the design and specifications were finalized, Excellerate built and shipped the duct bank in six weeks, where it could be essentially dropped into place and connected. Another benefit of the work of Excellerate was that project waste and scrap materials were kept from the jobsite and more easily recycled.
Children’s new generator facility was designed with three 15KV Caterpillar generators to replace five smaller units, generating 2.5 megawatts (MW) of power. Our project team took on the challenges that accompanied power generation of this size and voltage, including design of exceptionally large conduits with limited bending capacity, and these capabilities were built into the install planning. Excavation for the duct banks was completed in small sections done quickly, with less environmental impact.
Managing noise and exhaust was critical to Children’s. FTI worked with the owner and other partners to design and install noise dampening and exhaust mitigation for the new generators. The muffler and sound bars are designed to bring the sound down to 85 decibels, reducing to 55 decibels at Wisconsin Avenue, the closest public thoroughfare. The design proved valid, and the volume at the plant is even lower than targeted.
Fuel storage was moved underground and removed from the direct hospital building. Environmental impact studies were done to ensure exhaust levels for the new generator units are appropriate and are evacuated out of the facility properly, with no impact to nearby homes or businesses. The plant’s exhaust routes up through Children’s employee parking structure, moving it nine stories up, and away from pedestrian traffic and Corporate Center air intake.
As a trusted partner of Children’s, FTI worked extremely closely with the hospital’s Facilities team, seeing what their day-to-day needs were, as well as how they responded to power emergencies. Centralizing all their power generation in one location provides more seamless operations for them, with the ability to attend to all generators in one place rather than traveling across the campus. The new generators provide safe power backup for every square inch of their buildings in one place that can be easily maintained, which directly affects the safety of their patients and families.
Through our long-term relationship with Children’s and in-depth knowledge of their facilities, FTI was able to use current building infrastructure to provide temporary power needs during required power outages. This enabled us to minimize the purchase of temporary power generators and the fuel to run them, saving them budget dollars. FTI also found a buyer for the two old generators which were removed from the hospital and coordinated the transaction, repurposing the units and keeping them out of the landfill while provided monetary value to Children’s.
Children’s Wisconsin is a long-standing customer of FTI, and we’re thankful for the trust they put in us. We were proud to partner on this important project, which received recognition from Associated General Contractors (AGC) of Wisconsin with a BUILD Wisconsin award, and from Associated Builders and Contractors (ABC) of Wisconsin as a Project of Distinction.
If you enjoyed this blog article, please subscribe to stay up to date on the latest industry news from our experts at FTI.