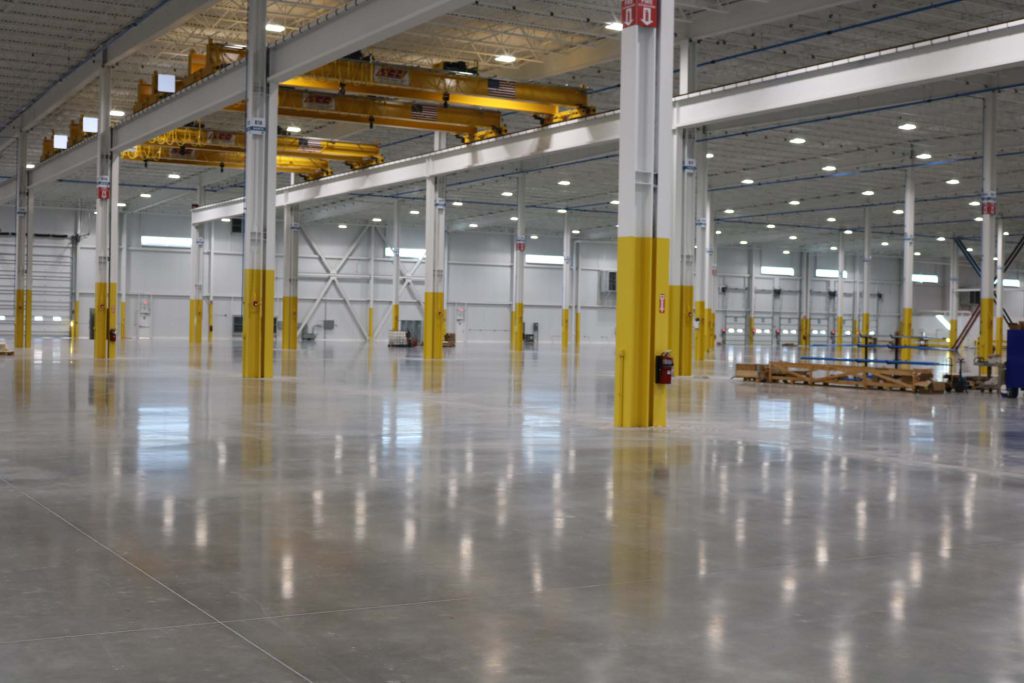
Overview: New Smart Manufacturing Facility Using Clean Technologies
FTI built a new Excellerate facility in Little Chute, Wisconsin. The 385,000-square-foot smart manufacturing facility project began in November 2022 and was completed in November 2023. The facility uses clean energy technologies to lower carbon emissions with the goal of reaching net zero energy in the future.
Work within the facility is concentrated on constructing modular electrical buildings (MEBs), which are fully integrated electrical modules used in the rapidly growing data center market. MEBs are fully self-contained electrical units that can be quickly deployed into data centers, eliminating most on-site electrical work. The facility also supports the continued growth of renewable energy technologies.
FTI worked with The Boldt Company as the general contractor and McMahon Associates as the engineer. They self-performed electrical, low voltage and systems work such as fire suppression, access controls and security systems throughout the manufacturing facility and administrative offices.
FTI incorporated complete end-to-end solutions including design, engineering, electrical manufacturing and construction. FTI ICIAN™ specialists were part of this build, and other ICIANs supported the ongoing energy and technology optimization.
Challenges: Logistics Challenges & Schedule Demands
The size of this building brought logistical challenges. The facility has four crane bays spaced throughout the facility, along with flexibility for multiple and overlapping customer/products. The 60- and 30-ton crane bays are rated for safety. FTI had to consider the location of support beams for these cranes. The facility was also built to accommodate drive-through capability for semi-trucks.
An accelerated schedule was also a challenge when faced with material delays and scope changes. The team developed ways to use off-the-shelf gear and manage the procurement process to hold to the original finish date.
Solution: eHouse Capabilities & Energy Modeling
FTI implemented an ehouse for the electrical installation, enabling completion of electrical work concurrent with the early building frame-up. This also enabled FTI to demonstrate ehouse capabilities to customers. The manufacturing floor was specially designed to support operation of air skate systems to move large-scale manufactured products safely and efficiently.
Energy modeling was incorporated for appropriate renewable resources such as microgrids and distributed energy resources. With the near-future installation of a microgrid, the facility will operate at net-zero energy in the next year. Electric vehicle (EV) chargers were also installed to accommodate FTI’s EV fleet and EVs of customers and team members.
FTI’s Excellerate work has been growing exponentially over the past several years as customers realize the value of high-quality modular work. By moving electrical work to a controlled manufacturing environment, FTI saves partners time and money, while providing the safest, most productive workspace for team members.